MiniPat Vertical Carousel
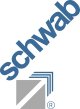
Carriers (shelves) are connected to transport chains that rotate the entire stored inventory around inside a steel clad casing in either direction working on the shortest routing principle to deliver the requested items at an ergonomic height to the operator.
The carriers are presented at the access port in front of the operator at a picking / placing height, usually 900mm, depending on the pitch of the carriers.
Intermediate carrier levels can be installed at any time to cater for small parts in bins etc. Multiple levels can be configured to meet the desired volume criteria.
The picking port working area is illuminated by directional low voltage LED
Schwab Tower Heavy Duty Lift

Schwab Tower is a vertical Lift capable of storing a wide variety of products such as steel or aluminium sheet and profiles, tooling, jigs, large, heavy and "ugly" parts etc. The Tower cassette can support a load of up to 5,000Kg each with variable size possibilities up to 12,000mm wide by 2,000mm depth with machine heights up to 16 metres.
The Tower crane can also be designed to travel laterally where such a configuration makes better use of the available floor space.
Unlike conventional vertical lift systems a Tower can also be configured in a multi stack version.
This has the benefit of accommodating a larger number of trays where required whilst still operating with one lift mechanism.
Schwab Multi-loop Paternosters

Steel carriers are connected to transport chains that rotate the entire complement of carriers around inside a framework in either direction working on the shortest routing path principle.
The required carrier is presented at the access port in front of the operator at an ergonomic working height.
Goods presentation can be brought forward of the framework to a loading nose arrangement allowing free access for manual picking or by Fork Lift Truck, Overhead Crane etc.
Products can be delivered to the front, rear or both, mezzanine floor and basement levels or in any combination of these.
Aids to greater efficiency
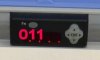
Being able to make the most efficient use of your space is only part of the solution to effective stock handling. It is also vitally important that you are able to locate and retrieve stock in a timely manner.
Additional equipment such as barcode readers and printers can greatly simplify the identification of stock to prevent miss-picks and similar errors. But this is only part of the solution...
Even greater savings can be made by using 'Batch Picking' where a number of orders are satisfied in parallel guided by 'Put to Light' indicators against the receiving bins.
Other Storage Systems
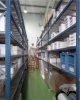
As part of our overall product portfolio and to provide our clients with the complete solution (new stores or warehouses will rarely use only automated storage) we also provide a comprehensive range of conventional storage and handling systems to complete the full requirement.
We can provide pallet racking to suit any application, from wide aisle, narrow aisle to mobiles, the right systems are chosen to meet storage and space criteria.
It's all supplied and installed to the latest standards to ensure that your staff and stock enjoy a happy and safe coexistence.
Storage Automation
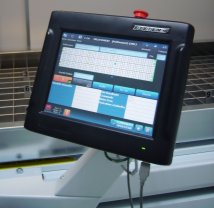
Efficient use of space for storing stock is only one way of reducing costs. While stock is in storage it is tying up capital and not earning a profit (unless it's fine wines or Old Masters).
So, as well as keeping stock to a sensible minimum, it is also vitally important that it can be handled efficiently, and methods for moving stock in and out of store must be effective. Couzens can supply associated accessories that address both of these problems.
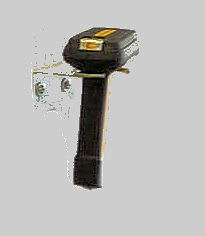
Storing
On receiving new stock, it must be possible to quickly route it directly to its point of use or find space to store it.
The routing can be accomplished through links to your company's main MRP or ERP system. Bar code printers can be used to label the items so that they can be tracked as they move around the site.
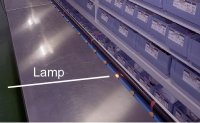
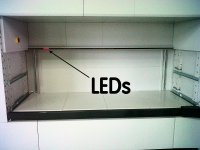
When the items need to be stored, the software will help to choose a suitable location. This can decision can be based on quantity, size and weight. It is then important that chosen location can be found quickly and accurately. Automated storage machines such as carousels or lifts will quickly bring the selected tray to the operator and, with the addition of indicator lights and on screen instruction, the item can be placed in the correct place. This can be confirmed by scanning bar codes on the item and the location as a double check.
Items stored in the wrong location can cause extremely costly delays when trying to find them.
Picking
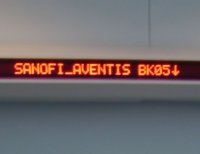
When stock is required from storage, it must be possible to locate it quickly and efficiently as possible and feed it to the required point of use or despatch.
The light or LED indicators shown above can provide part of the solution together with guiding on-screen displays. Bar code readers can again be used to confirm that the correct items have been selected.
Batch Picking
Even greater efficiency can be had by picking a number of orders at the same time, sometimes known as 'Batch Picking'. This is achieved by using additional indicators for the receiving bins. Picking orders in parallel results in fewer movements of carousels and lifts and thus reduces the time that an operator must wait.

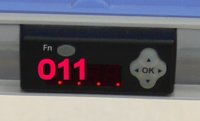
The above illustration shows three tote bins with their Put-To-Light displays. The indicators show how many of the item should be placed in each bin. The buttons at the right hand side of the display can be used to indicate that more (or less) items were supplied and to confirm that they have been placed in the bin
Only three bins are shown here, but larger numbers of between 5 and 10 per station have proved to be most efficient.
The 'Put' station can be located between a number of machines to provide 'Parallel Picking' so that stock can be taken from one machine while the others are fetching the next items.
Software
While it's important to know where your stock is, it's just as important to know where there is space for more and how many you've actually got. Couple that with the intelligence to be able to calculate the best picking route for, conveyors, operators and lift trucks and you get a really efficient warehouse.
Order tracking, inventory management and reports, FIFO, batch traceability and much more can be provided.
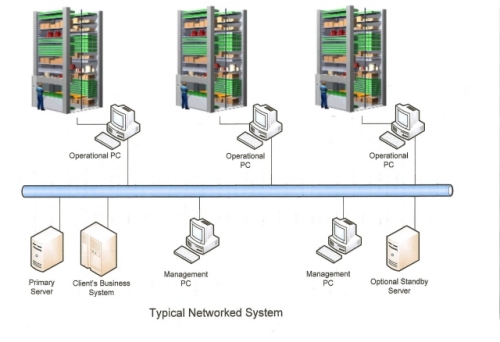